Is A Factory-Built Home Addition Right For You?
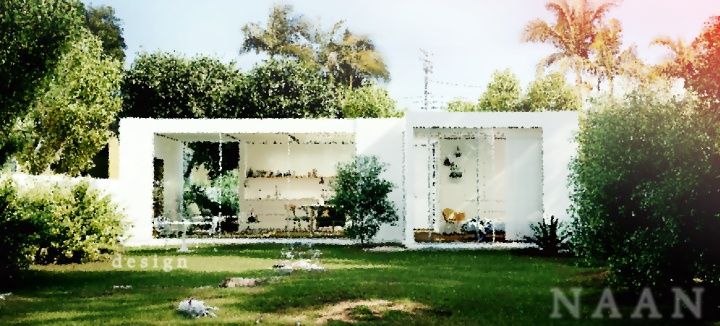
It's possible that a prefabricated, factory-built home addition could be right for you. An interesting option for an addition to the back of your house.
Are you considering an addition for back the of your house?
Many homeowners seek to improve their property by adding accessory structures. Accessory structures can increase property value by enhancing use of the land. Whether it's a home addition, shop, barn, office or in-law unit, the traditional path is to design and build a structure on the site from the ground up.
However, there is a new way to accomplish this task, and that is to use a prefabricated structure.
You might be picturing the large storage sheds that can be found on sale at your local big-box home improvement store. These can be useful, but are very limited in their function.
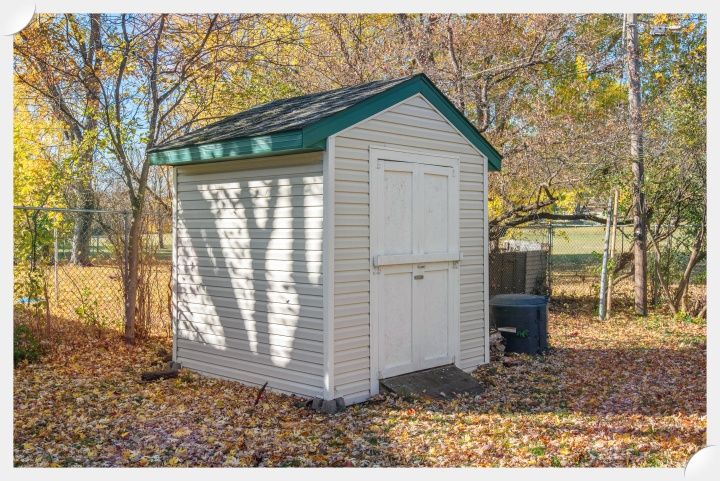
Changes have been made in California laws.
Changes have been made in California laws that allow for the addition of small units on the back of home lots. This is great news for many property owners, particularly in Southern California.
Other states in the USA may be more flexible in regards to extra dwelling units, but the technology being discussed here will apply to anyone who is interested in getting more out of their property and who wants to create an added space for visitors, family, or themselves.
The question is whether a prefabricated structure is right for you. This article is intended to help you understand the possibilities and better decide.
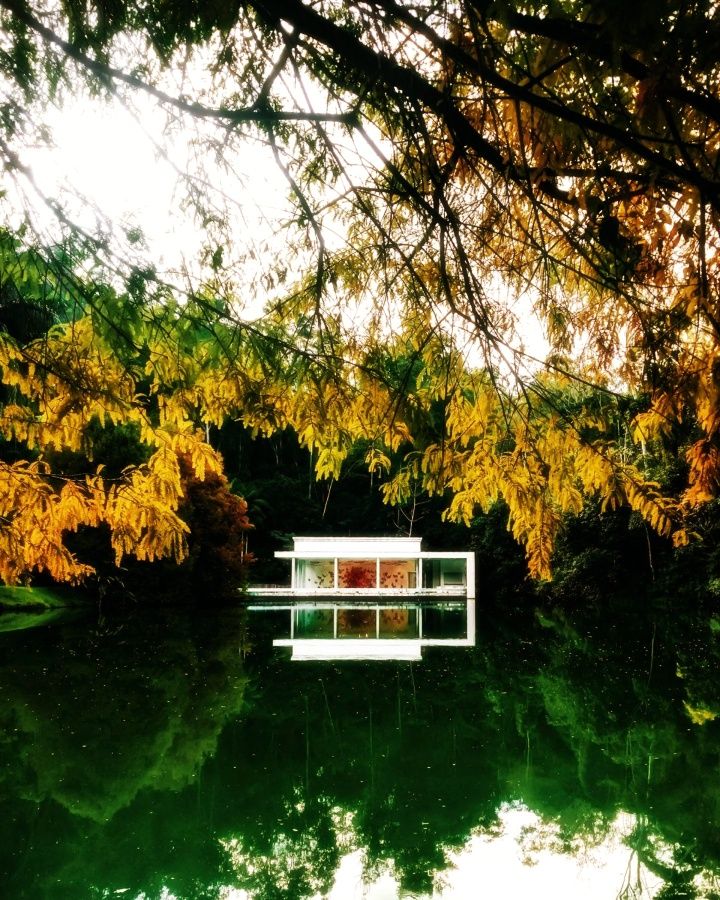
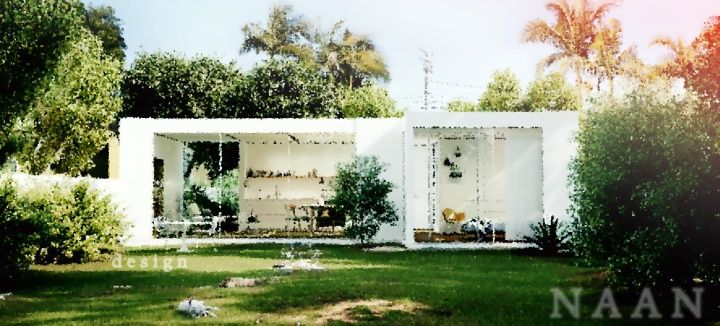
This post focuses on Cover.
Cover is an innovative Southern California company called that uniquely solves the problem of quality backyard home additions. The company designs and builds structures that take advantage of the efficiency and portability of storage sheds, while bringing a much higher level of design, finish and systems integration.
Benefits a prefabricated addition.
Explore prefab additions on AmazonWhat are the benefits of using a prefabrication?
According to Cover the benefits are many. The fact that most of the building can be assembled in a factory allows for design and construction innovations that are not available to standard construction methods.
The use of a factory makes it possible to integrate many systems at the same time.
Watch the video about Cover by Kirsten Dirksen.
The usual construction process.
The usual construction process is step-by-step with one trade completing their work before the next trade can begin. This standard of building on-site is labor and time intensive, and it is subject to a number of variables.
These variables , like weather, material availability, and scheduling conflicts, can delay the construction process wasting time and money.

Home: A Short History of an Idea
Walk through five centuries of homes both great and small
How is a prefabricated home addition different?
A factory-built project can proceed at a rapid pace with the potential to create a full enclosure on site within a 48-hour period.
Like a traditional home project, a foundation will need to be provided for the prefabricated structures. This would be likely be built with conventional methods. However, once the foundation is in place, a project can proceed at a rapid pace with the potential to create a full enclosure within a 48-hour period.
Thanks to building in a factory, Cover can create ready-to-assemble wall and roof pieces that are delivered to the site by truck.
Building components are made in a factory.
Because the building components are made in a factory, they will arrive on the site with many systems in place. These wall and roof panels simply need to be set in the correct location and connected together. Using Cover’s system, a typical prefabricated wall panel will include interior and exterior finishes, windows and doors, as well as insulation, plumbing, electrical, and HVAC systems. This makes the time on the site very fast requiring only a few interconnections.
Weather is no longer a factor in the production of these panels.
Panels can be easily built by teams with building inspections occurring on the factory floor before arriving on site. Construction noise is contained within the factory walls instead of the job site which reduces the environmental impact.
This panel system of construction has enabled significant door and window improvements. Windows and doors can be made frameless and run from the floor to the ceiling improving light access and the qualities of space. Sliding glass doors have the rollers in the frame, instead of on the door, which makes them light, quiet and operable with only a light touch
There is more to describe, but it may be best to watch the video above and see these items in action.
Who is Cover and what do they build?
The mission of Cover is to provide thoughtfully designed and well built home additions in the back of the house or anywhere else on site. Using the factory construction methods makes this very possible. System-based components can be adapted to the site and client needs and built with great precision. We admire the team and appreciate the efforts of Cover and their willingness to bring greater innovation to the built world.
Extra benefits to building a house addition this way.
One superb benefit of prefabricated building methods is that of being a good neighbor.
Having lived in the same neighborhood for over 20 years, 7 immediate neighbors have completed major home remodels. Each of these remodels and additions to the back of the house were built with conventional construction methods, and the average project completion time was one year.
That means that 7 of our 21 years, or 33% of the time, the neighborhood had to deal with the noise, mess, and general chaos of the standard construction process.
Had these projects been undertaken with prefabrication methods as championed by Cover, it could have been possible to reduce the construction time to 3 months per project.
This means it would have taken less that 2 years to complete all of them. That would amount to giving the neighborhood 5 more years of peace and quiet. Ninety percent of the time life would be normal on normal street, and everyone would appreciated that.
Thank you to Kirsten Dirksen and her crew for the excellent research and video work.
boilerplate.
Note: The content we provide is for education and entertainment purposes only. None of this is intended as health, life or financial advice. We don’t claim to be experts. We believe in lifelong learning and continuous education. As always, it is suggested that you do your own research [DYOR].
Affiliate Disclosure: This is a reader-supported publication. See the Privacy policy for full affiliate disclosure details. In a nutshell, we might receive a small commission from the links we are providing. There is no cost to you, and this has no impact on your price. Our goal is to find the best deals for you. Links are provided mainly for convenience to help you quickly find the items being described and discussed. Purchases are made at your own discretion.